Compressor maintenance is a fundamental aspect of ensuring the longevity, efficiency, and safety of power equipment. Compressors are critical components in various industrial processes, powering pneumatic tools, and ensuring the smooth operation of machinery. However, like any complex machinery, compressors require regular maintenance to function at their best. This maintenance not only focuses on the compressor itself but also extends to the entire pneumatic network, including filters, piping systems, hoses, valves, dryers, and receivers. Given the complexity and importance of these tasks, it is often advisable to entrust the maintenance process to professionals, such as those from a marine engineering company, who possess the necessary expertise and tools.
The Importance of Compressor Maintenance
Regular maintenance of compressors is essential for several reasons:
- Preventing Downtime: A well-maintained compressor is less likely to break down unexpectedly, reducing the risk of costly downtime in production processes. Unplanned outages can disrupt operations, leading to significant financial losses.
- Extending Equipment Life: Proper maintenance ensures that the compressor and its components are in good working order, which can significantly extend the life of the equipment. This means lower replacement costs and better return on investment.
- Ensuring Safety: Compressors operate under high pressure, and any malfunction can pose serious safety risks. Regular inspections and maintenance help identify and mitigate potential hazards, ensuring the safety of personnel and equipment.
- Maintaining Efficiency: Over time, wear and tear can reduce the efficiency of a compressor. Regular maintenance helps keep the compressor running at optimal efficiency, reducing energy consumption and operational costs.
- Compliance with Regulations: In many industries, regular maintenance of compressors is required to comply with safety and environmental regulations. Adhering to these requirements is crucial to avoid fines and legal issues.
Understanding Scheduled Compressor Maintenance
Scheduled compressor maintenance refers to a pre-planned set of activities aimed at maintaining the operability of the equipment and extending its service life. This type of maintenance is typically carried out at regular intervals or after the compressor has operated for a certain number of hours. There are three primary types of compressor maintenance:
- Scheduled Maintenance (Regulated): Scheduled maintenance is the cornerstone of compressor care. It involves a structured plan and schedule, drawn up and approved after the compressor is put into operation. This plan considers the manufacturer’s recommendations, the specific operating conditions, and the design features of the compressor units. Scheduled maintenance is crucial for preventing unexpected failures and ensuring the equipment runs smoothly.
- Unscheduled Maintenance: This type of maintenance is performed in response to an unforeseen event, such as a sudden breakdown or malfunction. While unscheduled maintenance is necessary when issues arise, it is generally more costly and disruptive than scheduled maintenance. It often involves emergency repairs that can lead to extended downtime.
- Condition-Based Maintenance: Condition-based maintenance takes a more proactive approach. It involves continuously monitoring the compressor’s condition and performing maintenance based on real-time data and expert assessments. This type of maintenance can be more efficient than scheduled maintenance, as it focuses on actual wear and tear rather than predetermined intervals. However, it requires sophisticated monitoring systems and expertise to interpret the data correctly.
Key Considerations in Scheduled Maintenance
Scheduled maintenance activities are meticulously planned and executed to ensure the compressor’s reliability and efficiency. The schedule for these activities is drawn up in tandem with a preventive maintenance plan and approved by a responsible employee within the organization.
The maintenance schedule should include:
- Daily Maintenance: Routine checks and minor tasks that can be performed by the enterprise’s specialists.
- Monthly Maintenance: More in-depth inspections and maintenance tasks that require some technical knowledge.
- Annual or Semi-Annual Maintenance: Comprehensive checks and replacements, typically performed by qualified professionals.
Methods for Performing Scheduled Technical Inspections
Visual Inspection
Visual inspection is the most basic and essential method of compressor maintenance. It involves checking the condition of units, pipelines, and other components for visible signs of wear, damage, or leaks. Regular visual inspections can help identify issues early, allowing for timely repairs and preventing more severe problems down the line.
Technical Inspection
Technical inspection involves the use of specialized tools and instruments to measure and evaluate the performance of the compressor and associated equipment. This method provides a more detailed and accurate assessment of the equipment’s condition, allowing for precise maintenance actions. Technical inspections are typically performed by professionals with the necessary expertise and equipment.
Creating a Compressor Maintenance Plan
A comprehensive compressor maintenance plan divides tasks by their frequency and importance. The intervals for these tasks can range from daily checks to annual overhauls. Below is an expanded look at the maintenance tasks that should be included in a well-structured plan.
Daily Maintenance Tasks
Responsible Person: Specialists within the enterprise where the compressor is used.
Tasks Include:
- Frequency: Every 8-12 hours.
- Checking the Oil Level: Oil is crucial for lubricating the moving parts of the compressor, preventing excessive wear and tear. Regularly checking the oil level ensures that the compressor is properly lubricated.
- Inspecting for Oil Leaks: Leaks can lead to insufficient lubrication, causing damage to the compressor. Identifying and fixing leaks early is vital.
- Ensuring the Tightness of Threaded Connections on Hoses and Pipelines: Loose connections can lead to air leaks, reducing the efficiency of the compressor and potentially causing damage to the system.
- Checking and Draining Condensate as Necessary: Condensate can accumulate in the compressor and related components, leading to corrosion and other issues. Regularly draining condensate prevents these problems.
- Listening for Unusual Noises or Vibrations: Unusual sounds or vibrations can indicate underlying issues with the compressor. Identifying these signs early can prevent more serious problems.
- Monitoring the Condition and Readings of Sensors, Pressure Gauges, and the Thermostat: These devices provide essential information about the compressor’s operating conditions. Regular monitoring ensures that the compressor is operating within safe and efficient parameters.
- Visual Inspection for Any Damage: Regular visual checks for physical damage can help prevent more severe issues.
Monthly Maintenance Tasks
Responsible Person: Can be performed by in-house staff or maintenance professionals, depending on the complexity.
Tasks Include:
- Detailed Inspection of All Components: A thorough inspection helps identify any wear, damage, or other issues that may have developed over time.
- Cleaning Dust and Debris from the Equipment: Dust and debris can accumulate on the compressor, leading to overheating and reduced efficiency. Regular cleaning helps maintain optimal performance.
- Checking and Replacing Filters if Necessary: Filters play a crucial role in keeping the air clean and preventing contaminants from entering the system. Regularly checking and replacing filters ensures the compressor runs smoothly.
- Inspecting and Tightening All Connections: Regular inspection and tightening of connections help prevent leaks and ensure the system’s integrity.
- Checking the Electrical Components and Ensuring They are Functioning Properly: Electrical issues can cause the compressor to malfunction or even fail. Regular checks ensure that all electrical components are in good working order.
- Examining the Drive Belt for Wear and Tension: The drive belt is a critical component of the compressor. Regular inspection and adjustment ensure it remains in good condition and functions properly.
Annual Maintenance Tasks:
Responsible Person: Qualified maintenance professionals.
Tasks Include:
- Replacing Seals, Gaskets, and Bearings: These components can wear out over time, leading to leaks and other issues. Regular replacement helps maintain the compressor’s performance.
- Inspecting and, if Necessary, Replacing the Radiator: The radiator helps cool the compressor, preventing overheating. Regular inspection and maintenance ensure it functions properly.
- Comprehensive Electrical Inspection: Electrical components can degrade over time, leading to malfunctions. A thorough inspection ensures that all components are in good condition.
- Testing the Overall System for Performance and Efficiency: Regular testing helps identify any issues with the compressor’s performance, allowing for timely repairs or adjustments.
- Calibration of Pressure Gauges and Other Monitoring Devices: Accurate measurements are essential for maintaining the compressor’s performance. Regular calibration ensures that all devices provide accurate readings.
The Role of Professional Maintenance
While daily and monthly maintenance tasks can often be handled by the enterprise’s staff, complex maintenance work should be left to qualified professionals. This includes replacing critical components like filters, seals, and bearings, as well as inspecting and repairing electrical equipment. Professionals bring a level of expertise and precision that is often necessary for maintaining the compressor in peak condition.
Why Professional Maintenance is Essential:
- Expertise: Professionals have the knowledge and experience to handle complex maintenance tasks that require specialized skills and tools.
- Precision: Professional maintenance ensures that all components are properly serviced, preventing issues that could arise from improper handling.
- Compliance: Professional maintenance services are often necessary to meet regulatory requirements, ensuring that the compressor operates safely and efficiently.
- Cost-Effectiveness: While professional services may seem costly upfront, they can save money in the long run by preventing costly breakdowns and extending the equipment’s life.
Conclusion
Regular and thorough compressor maintenance is vital for the reliable operation of pneumatic systems. By adhering to a well-structured maintenance plan, which includes daily, monthly, and annual tasks, and by utilizing professional services for complex maintenance, businesses can significantly enhance the performance and longevity of their compressor equipment. Entrusting this task to experienced professionals, such as those from marine engineering companies, ensures that all aspects of the maintenance process are handled with the utmost precision and care.
In a world where equipment reliability and efficiency are paramount, investing in regular compressor maintenance is not just a good practice—it’s a necessity. Properly maintained compressors not only operate more efficiently and last longer but also contribute to safer and more reliable industrial operations.
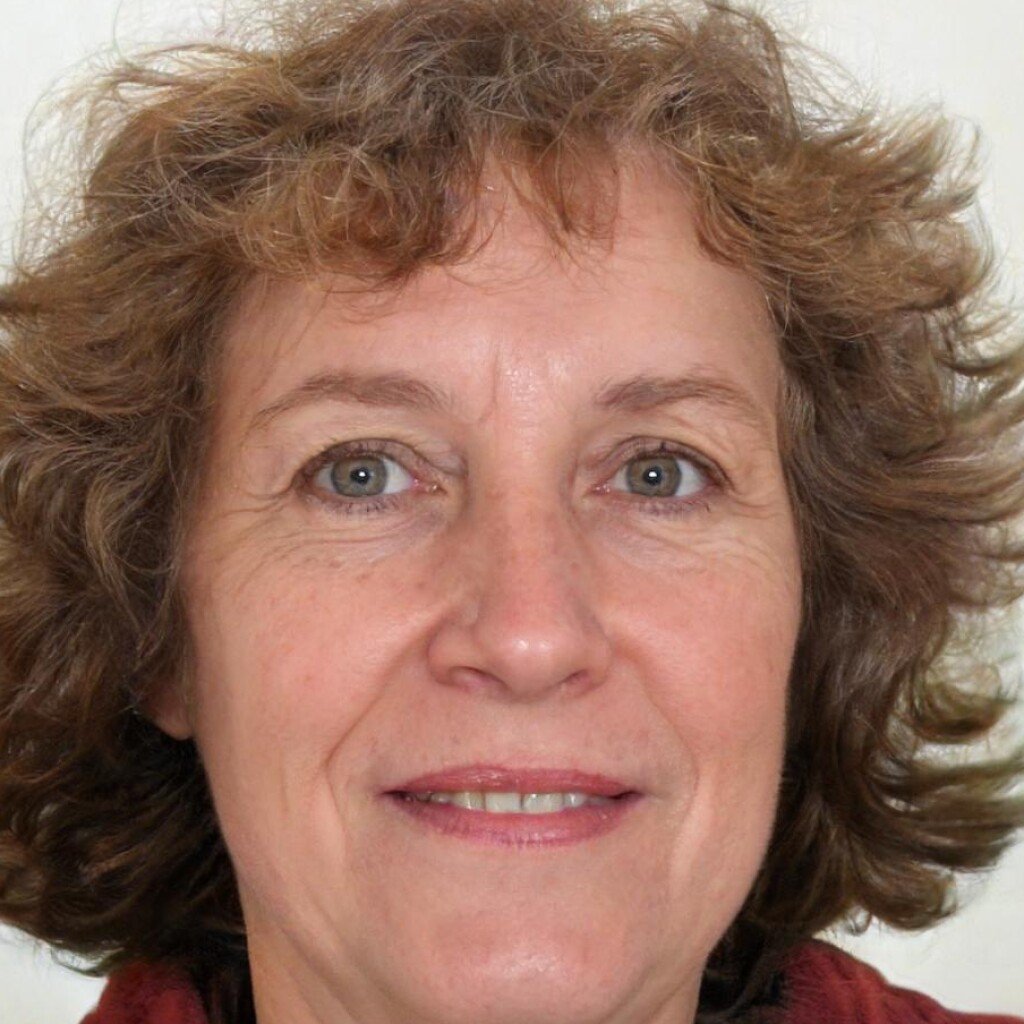
Snowboarder, risk-taker, ukulelist, Eames fan and typography affectionado. Acting at the crossroads of beauty and mathematics to craft experiences that go beyond design. I prefer clear logic to decoration.